Die-casting moulds made of refractory metals
Moulds are exposed to high stresses
In order for castings to be manufactured with the highest precision, the appropriate die-casting moulds are needed. And there are high-performance metals for this! Tungsten, tungsten-copper, tungsten-heavy metal, niobium, tantalum, molybdenum and alloys with these refractory metals provide important prerequisites for technical progress. This is because refractory metals are particularly resistant to wear and high temperatures. The thermal and mechanical resilience makes them ideal for the production of moulds for metallurgical processes.
It is impossible to imagine production lines without tungsten & Co.: due to the materials’ high melting temperature, the die-casting moulds remain stable and do not warp during the casting process. Precise dimensions are particularly important for components in the automotive industry: Each part must fit exactly. Compared to other mould materials, refractory metals offer a longer service life and can withstand high loads. Would you like to know more about the special properties of the various refractory metals?
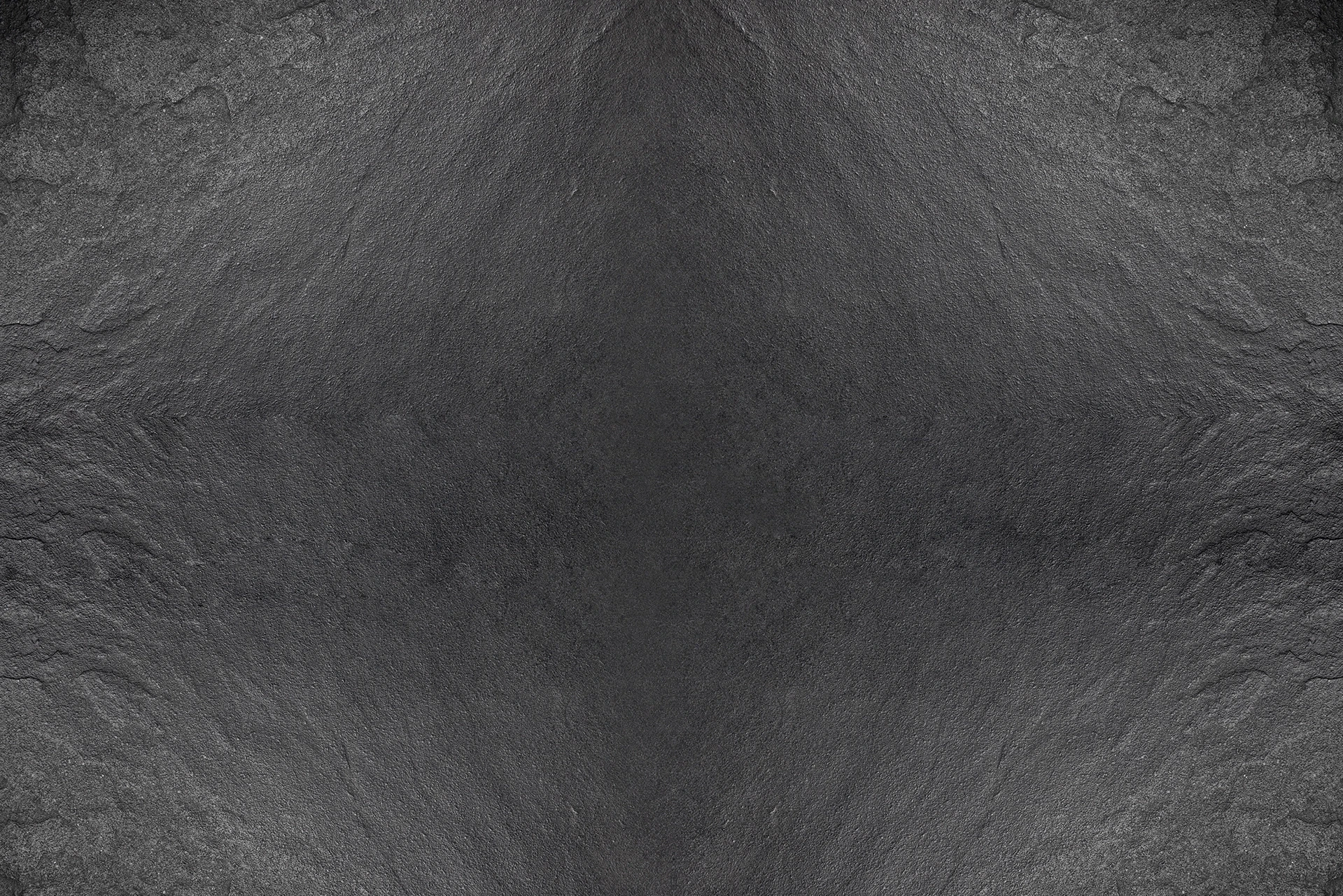
Use of refractory metals for die-casting
The durability makes die-casting moulds made of refractory metals popular for many industries. After all, the automotive, aerospace, medical and energy industries are just a few examples that require complex and accurate castings. Examples of use:
- Tools
- Engine parts
- Gearboxes
- Landing gear
- Combustion chambers
- Turbines
- Generators
- Engines
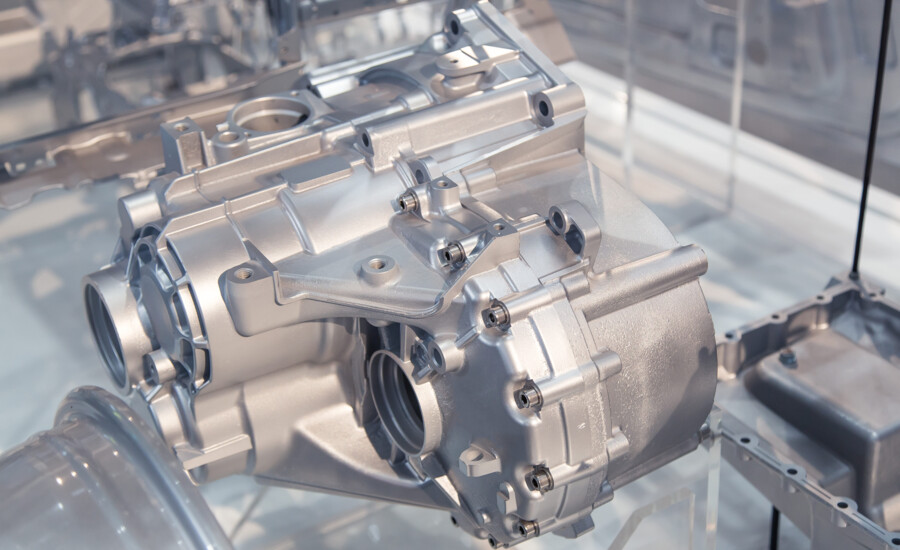
Die-casting moulds for extraordinary design
Another trend is the use of modern technologies such as 3D printing and CNC machining to make the manufacture of moulds even more precise and efficient. By using special technologies, moulds can be made that have complex geometric shapes and details. In addition, they are quicker to manufacture. This enables companies to develop innovative products that meet their customers’ requirements.
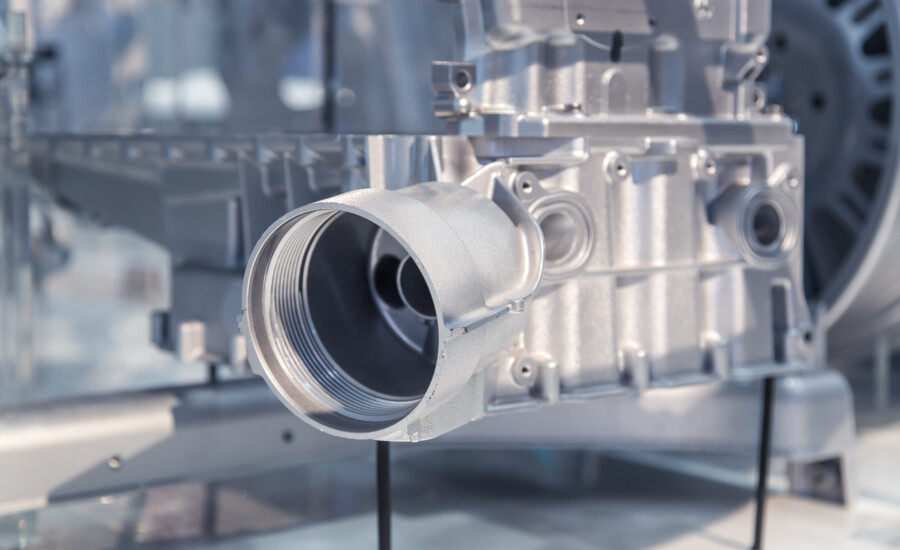
Good to know
There are two aspects to consider regarding the sustainability of die-casting moulds made from refractory metals: Firstly, materials from which the moulds are made can withstand several casting cycles. This means that they need to be replaced less often compared to other mould materials, resulting in reduced waste production. Secondly, the moulds can be recycled in various ways when they reach the end of their life.